Quality Assurance System
- Erik De Jong
- Apr 11
- 2 min read
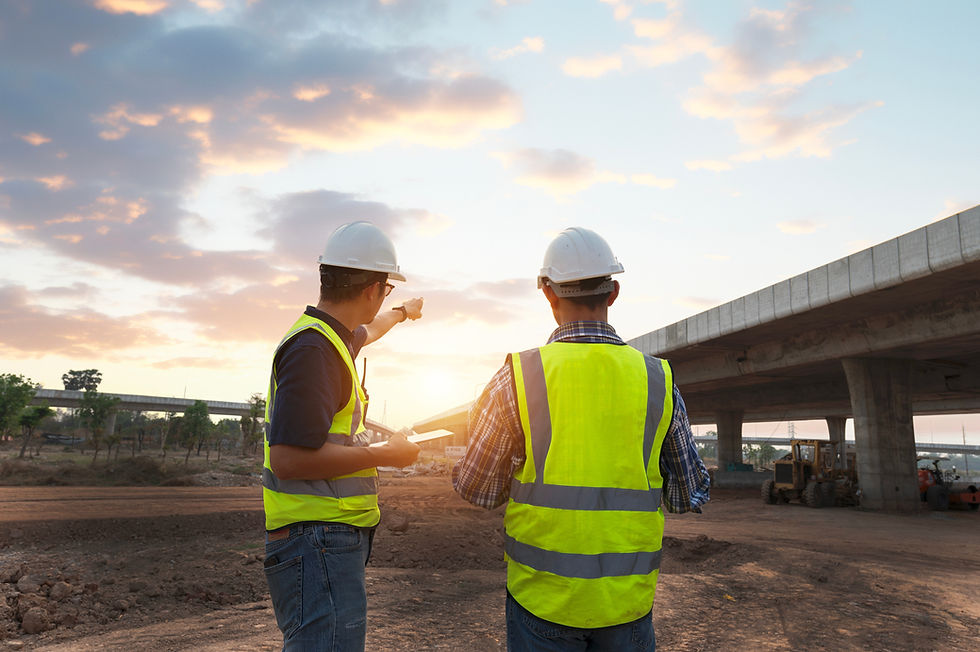
Overview
A quality assurance system is the set of processes, controls, and procedures an organization uses to ensure a high standard of products and services, focusing on preventing defects and improving processes to deliver high-quality outcomes consistently. In the broad strokes, a quality assurance system governs all aspects of an organization from hierarchy to employee training. To ensure product quality, particularly during day-to-day operations, periods of business expansion, or during the introduction of a new product, a quality assurance program must have the following elements:
Concise Standard Operating Procedures
Buy-in from all parties participating in the quality assurance program
Effective initial training
Continual learning methodologies
Quality checks
Effective and continuous system reviews
It is important to ensure a quality assurance program does not overburden organizations with bureaucracy or legalistic procedural methods that prevent operational specialists from autonomy, innovation, and practical implementation of their expertise.

SOPs
A Standard Operating Procedure (SOP) is a set of instructions that document a routine or repetitive activity followed by an organization. The development and use of SOPs are an integral part of a successful quality system as they provide individuals with the information to perform a job properly and facilitate operational standardization.

Participation
A successful quality assurance system relies on active participation from all parties involved — including management, supervisors, workers, subcontractors, and suppliers. Full engagement ensures consistent standards, reduces errors, improves efficiency, and builds long-term project and company credibility.

Implementation
The proper implementation of the quality assurance system places the well-fashioned SOPs and supporting systems into practice for the first time. All parties should already be aware of the procedures being implemented. The new or optimized procedures must fit well within the existing procedural eco-system. To ensure implementation, training should be provided to workers, suppliers, and subcontractors.
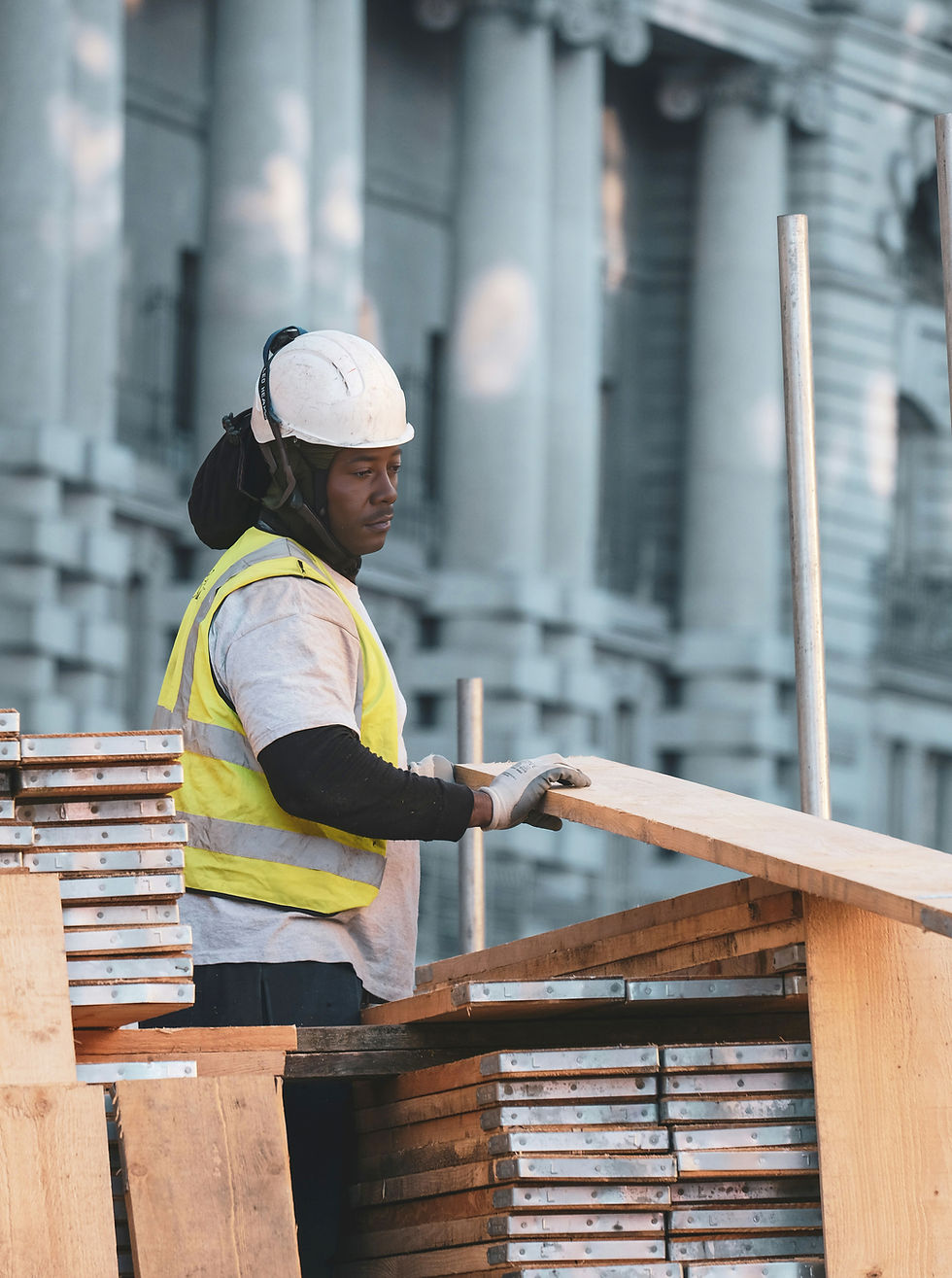
Continuation
Once the system has been implemented, a method for continuing the system in perpetuity must be implemented to ensure that the quality assurance system becomes merged with the organization itself. This includes:
training newly onboarded parties
continued or corrective training procedures
systematic organization
procedural reminders
employee and managerial accountability
both scheduled and randomized quality checks
The continued use of these methods will ensure the quality assurance system is of continued benefit to the organization.

Review
The quality assurance system must be reviewed continually to optimize its results and adapt to changing conditions. When conducting a review, important matters to consider are:
Procedures are being followed
Quality targets are met
Continuous improvement happens
Compliance with regulations, contracts, and client requirements
The concluded quality assurance system review should be documented to include the review’s scope, inspection procedures and metrics, the facts and data analyzed, the feedback parties provided, and the recommended improvements provided.
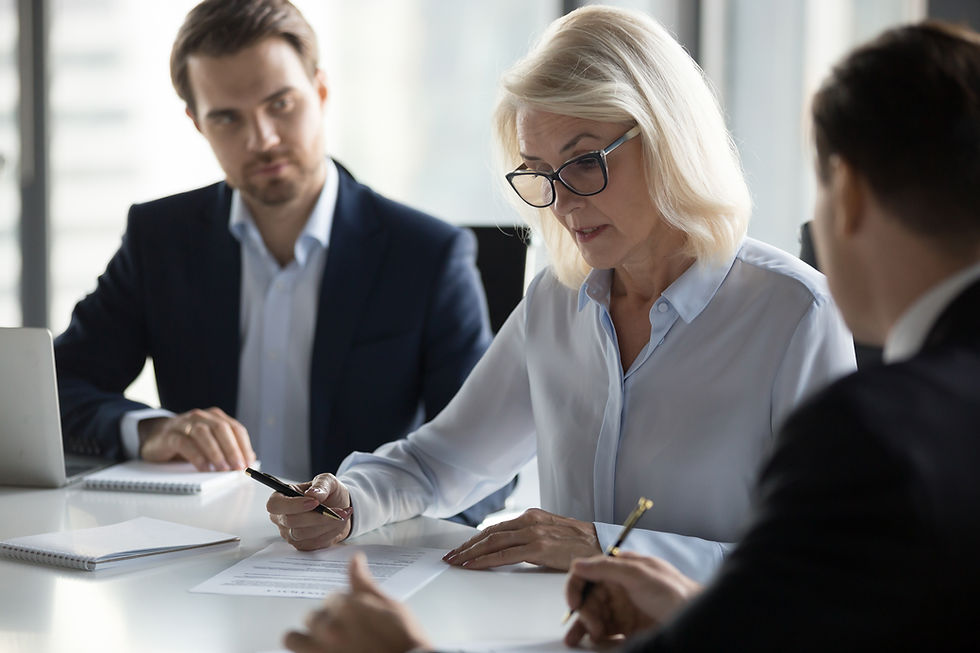
Conclusion
An effective quality assurance system will ensure a high standard of products or services are provided to clients while allowing an organization to operate at maximum efficiency and optimization.
For additional information or to partner with Mythetrix Consulting to create a quality assurance system specific to your needs, please contact Erik here or via social media.
Comments